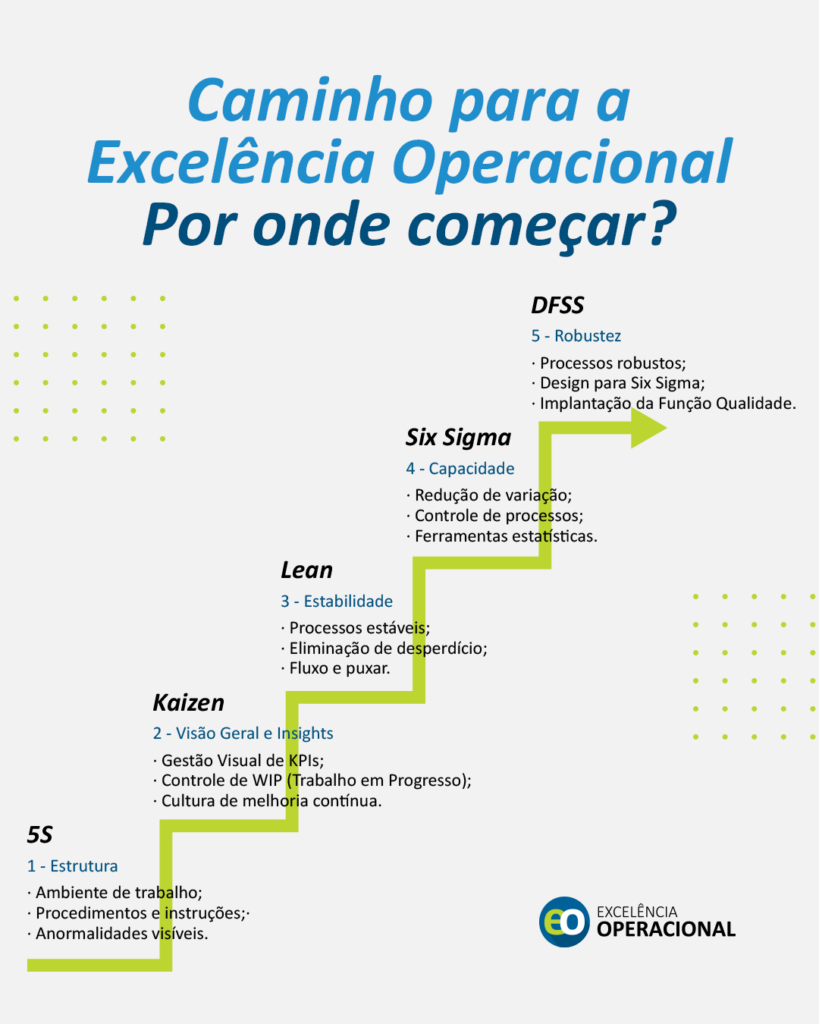
A busca pela excelência operacional é uma jornada estratégica que vai além da simples implementação de ferramentas e metodologias. Trata-se de criar uma cultura organizacional focada em melhoria contínua, estabilidade dos processos e entrega de valor ao cliente. Para alcançar esse objetivo, é fundamental seguir um roteiro estruturado que inicie pela organização básica do ambiente e evolua para processos robustos e eficientes.
Aqui está um passo a passo para orientar empresas nessa jornada, com exemplos práticos para ajudar no entendimento.
1. 5S – Estrutura
A base para qualquer transformação começa no chão de fábrica ou no escritório, com a aplicação da metodologia 5S: Seiri (organização), Seiton (ordem), Seiso (limpeza), Seiketsu (padronização) e Shitsuke (disciplina). O objetivo é criar um ambiente de trabalho organizado, seguro e visualmente agradável, permitindo que os problemas sejam identificados e corrigidos com rapidez.
Exemplo prático:
Uma indústria automotiva enfrentava atrasos na linha de montagem devido ao tempo perdido procurando ferramentas e peças. Após implementar o 5S, cada ferramenta foi identificada e alocada em um local fixo, com marcações visuais claras. O resultado foi uma redução de 30% no tempo de setup e um aumento na produtividade.
Principais benefícios:
- Ambiente de trabalho mais seguro, reduzindo acidentes.
- Procedimentos claros, reduzindo erros operacionais.
- Identificação rápida de anormalidades, como peças danificadas ou fora do lugar.
2. Kaizen – Visão Geral e Insights
Depois de criar uma base sólida com o 5S, a próxima etapa é adotar a filosofia Kaizen, que significa “mudança para melhor” em japonês. O Kaizen promove a melhoria contínua por meio de pequenos ajustes diários que, ao longo do tempo, resultam em grandes avanços.
Exemplo prático:
Uma padaria local aplicou o Kaizen para reduzir desperdícios na produção de pães. A equipe percebeu que os ingredientes eram frequentemente misturados em quantidades maiores do que o necessário, levando ao descarte de massa excedente. Com ajustes simples, como a padronização das receitas e o monitoramento visual de estoques, a padaria economizou 15% nos custos de produção.
Elementos essenciais do Kaizen:
- Gestão visual de KPIs: Exibir os indicadores de desempenho de forma clara, como gráficos de produtividade ou taxa de desperdício.
- Controle de WIP (Trabalho em Progresso): Reduzir estoques intermediários para evitar excesso de trabalho acumulado.
- Cultura de melhoria contínua: Envolver todos os níveis da organização na busca por melhorias.
3. Lean – Estabilidade
Com a cultura de melhoria contínua estabelecida, é hora de aplicar os conceitos Lean, que visam eliminar desperdícios e criar processos estáveis e enxutos. O Lean é especialmente poderoso em empresas que enfrentam gargalos ou produções desbalanceadas.
Exemplo prático:
Uma fábrica de móveis enfrentava atrasos devido ao transporte frequente de peças entre setores distantes. Após mapear o fluxo de valor, foi implementado um layout celular, agrupando máquinas próximas umas das outras. O tempo de produção de cada lote caiu de 5 dias para 2 dias, aumentando a capacidade de atendimento ao cliente.
Foco do Lean:
- Processos estáveis: Garantir que operações ocorram de maneira previsível e sem interrupções.
- Eliminação de desperdícios: Identificar e remover atividades que não agregam valor, como transporte excessivo ou retrabalho.
- Fluxo contínuo e puxado: Produzir de acordo com a demanda real, evitando estoques desnecessários.
4. Six Sigma – Capacidade
Com processos estáveis, o Six Sigma entra como uma abordagem científica para reduzir variações e aumentar a capacidade dos processos. Ele utiliza metodologias como DMAIC (Definir, Medir, Analisar, Melhorar e Controlar) e ferramentas estatísticas avançadas.
Exemplo prático:
Uma empresa farmacêutica utilizou o Six Sigma para melhorar a precisão no enchimento de frascos de medicamentos. Após uma análise estatística detalhada, ajustes foram feitos na configuração das máquinas de envase. A variabilidade no peso dos frascos foi reduzida em 50%, minimizando perdas e aumentando a conformidade com regulamentações.
Destaques do Six Sigma:
- Reduzir variação: Assegurar que os resultados estejam dentro de limites aceitáveis.
- Controlar processos: Implementar controles estatísticos para monitorar o desempenho.
- Ferramentas estatísticas: Usar gráficos de controle, análise de regressão e testes de hipóteses para solucionar problemas.
5. DFSS – Robustez
A última etapa, Design for Six Sigma (DFSS), foca na robustez dos processos e produtos desde a fase de concepção. É uma abordagem preventiva, garantindo que as falhas sejam evitadas antes mesmo de ocorrerem.
Exemplo prático:
Uma startup de tecnologia adotou o DFSS para projetar um novo aplicativo de gerenciamento financeiro. Durante o desenvolvimento, foram realizadas simulações para testar o comportamento do sistema sob diferentes condições de uso. O resultado foi um aplicativo confiável, com menos de 1% de taxa de falhas após o lançamento.
Componentes do DFSS:
- Design robusto: Produtos e processos projetados para resistir a variações externas.
- Função qualidade: Incorporar requisitos do cliente desde a concepção.
- Métodos preditivos: Usar ferramentas como análise FMEA (Análise de Modos de Falha e Efeitos) para prever e mitigar riscos.
Conclusão
O caminho para a excelência operacional é um processo iterativo que exige dedicação e disciplina. Cada etapa – do 5S à robustez do DFSS – desempenha um papel crucial na construção de uma organização eficiente e resiliente.
Os exemplos práticos apresentados mostram como empresas de diferentes setores podem aplicar essas metodologias para resolver problemas reais e alcançar resultados mensuráveis. Seja uma indústria de grande porte ou uma pequena empresa, o sucesso reside em começar com uma base sólida, envolver as pessoas certas e seguir consistentemente os passos rumo à excelência.
A excelência operacional não é apenas um objetivo; é um compromisso contínuo com a melhoria e a inovação. E agora, por onde você começará?